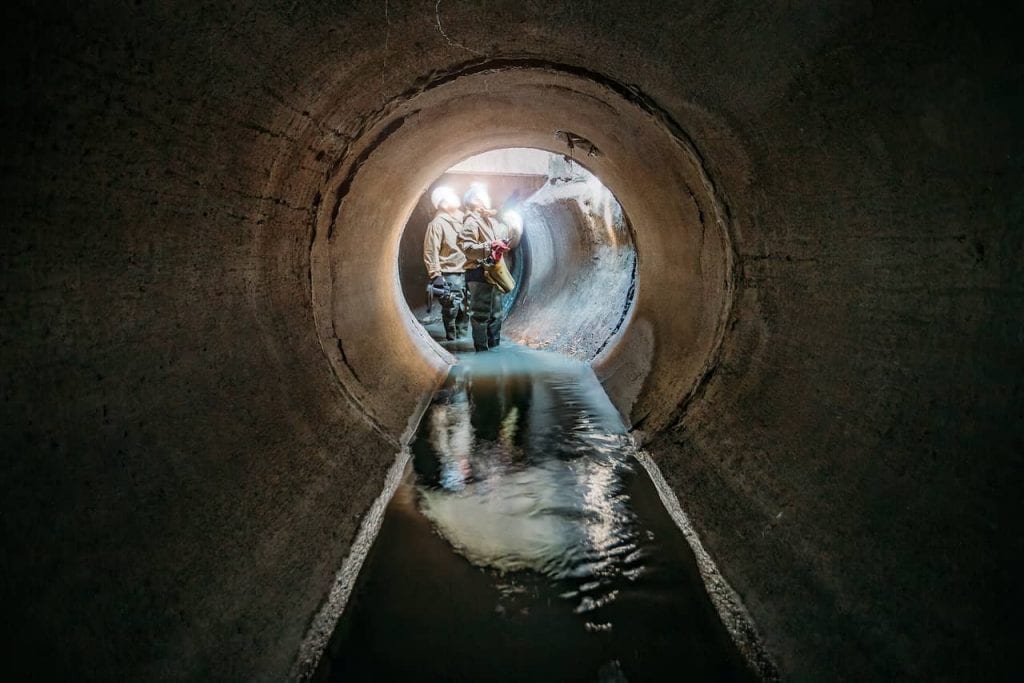
Why Go Trenchless?
Trenchless pipe lining, commonly referred to as trenchless pipe rehabilitation, is a growing innovative methodology to restore aged and deteriorated pipelines without digging. There are obvious advantages to this form of repair; the cost of trenchless pipe lining is typically far lower than digging and replacing the old pipeline. Many sewers, storm drains, and culverts were first installed in the early 20th century, with the above-ground changing significantly since. Neighborhoods, roads, and parks that did not exist years ago currently sit directly on top of the aging infrastructure.
Traditional Open-Cut Construction vs. Trenchless
Both traditional pipe repairs and trenchless pipe lining serve the same purpose — to restore deteriorated pipes. Nonetheless, the execution of each method varies widely.
Traditional dig and replace processes are generally useful. However, it is invasive with dig and replace or repair worksites disrupting the public. Likewise, the digging displaces the ecological environment. The process is typically more expensive and time intensive. On the other hand, trenchless pipe lining is an innovative, cost-effective, and ecologically forward solution to renew pipes.
Eco-Friendly Construction
With these methods the surrounding landscape and related ecosystems are left undisturbed. This means that roads, lawns, medians, parks, and other areas are able to maintain their integrity. Certain trenchless pipe lining methods are capable of fully restoring pipelines without harmful or odorous chemicals. This mitigates any concern of contamination or needing to contain the use of these substances. Trenchless pipeline repair methods eliminate the need for heavy machinery as well as large construction mobilization. Instead, the equipment needed is often more compact with decreased carbon emissions and less need for fuel/thermal processes.
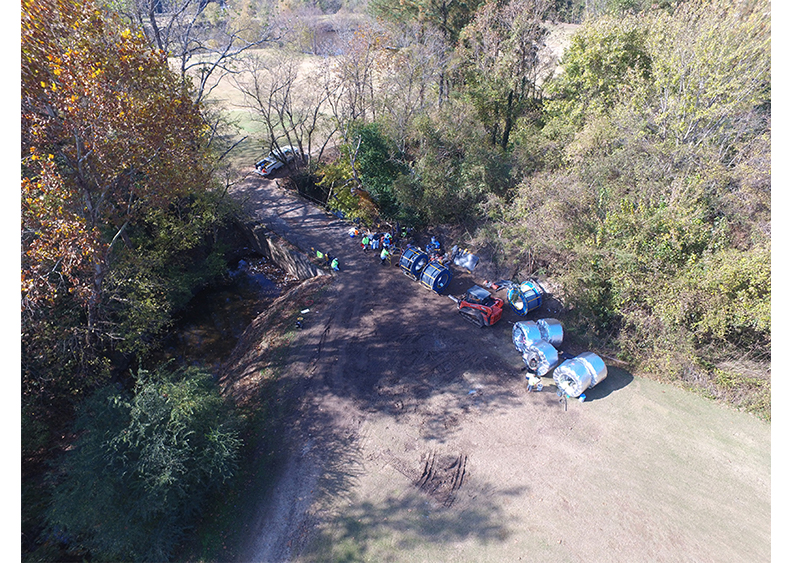
Pipe Applications
The wonderful thing about trenchless technology is that it serves nearly every type of pipe application available. Some methods may cover certain applications, such as focusing on gravity pipelines between a certain diameter (methods covered in next section). Utilize our trenchless calculator tool to see if Spiral Wound is a good fit for your pipe rehabilitation project.

Trenchless lining methods serve pipe diameters ranging as small as 2″ to well over 200″. These technologies are used to renew pipeline systems that consist of concrete, brick, CMP, clay, steel, PVC and others. Trenchless is applicable for gravity sewer, storm drains, culverts as well as pressure pipes such as water, sewer, oil and gas. The different trenchless lining methods focus on different types of pipe applications, which will be focused on in the next section.
Another factor for pipe applications is the shape of the pipe. Larger pipes often come in a variety of shapes such as a box, horseshoe, egg, teardrop, etc. Many pipelines also have unique alignments such as bends. Not all trenchless methods can renew non-round shapes or bends but for a select few.
Trenchless Methods Available
Some of the primary trenchless pipe lining methods include spiral wound lining, cured-in-place pipe (CIPP), slip-lining, pipe bursting, and spray-in-place pipe (SIPP). These rehabilitation methods vary by material and installation process.
Spiral Wound Lining
Spiral Wound mechanically installs a wound PVC liner inside a pipe. The process can be installed in live flow and is fully structural. Spiral Wound is applicable for gravity sewer, storm drains and culverts. The wound PVC profile slightly reduces the ID of the host pipe, however, the hydraulic capacity of PVC (Manning’s Coefficient of .009) typically makes up for this loss.
- 6″ – 200″+
- Fully Structural
- Gravity Pipe
- Mechanical Process
- Live Flow Lining
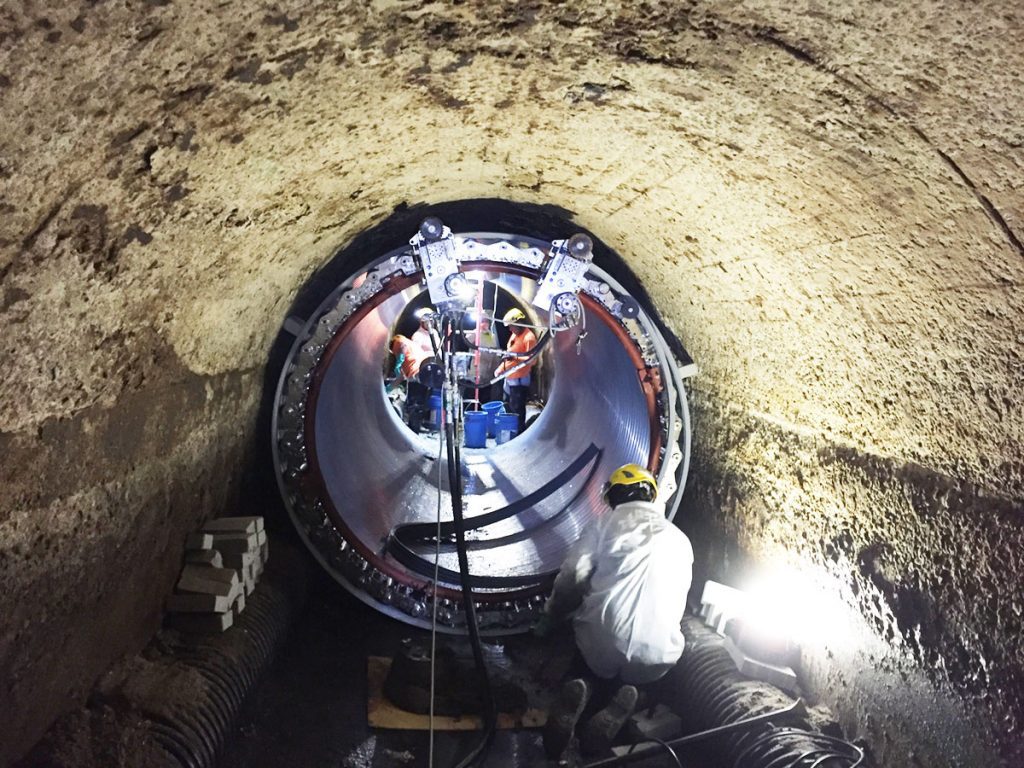
Cured-in-Place Pipe (CIPP)
CIPP is a resin-impregnated tube that is inserted or pulled and subsequently cured in place to form a pipe within a pipe. It is another fully structural solution. This method is used on both gravity and pressure pipe applications. CIPP is offered in a number of forms that vary from the types of resin used (vynelster, epoxy, etc.) to the installation/curing method (heat, steam, tower, UV).
- 2″ – 108″
- Fully Structural
- Gravity & Pressure Pipe
- Resin Curing Process
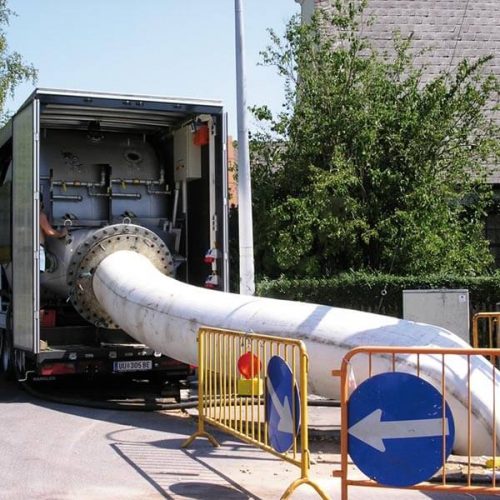
Sliplining
Sliplining slides a flexible, slightly reduced diameter pipe within the existing pipe. The space between the liner and pipe is grouted. The pipe inserted within the existing line is a new, typically HDPE pipeline. With the installation process not requiring a dry pipe, sliplining can be conducted within live flow. Since a new pipe is being inserted, the existing line must be thoroughly cleaned and cleared of any debris.
- 4″ – 150″
- Fully Structural
- Gravity & Pressure Pipe
- New HDPE/PE/FRP/PVC Pipe
- Live Flow Lining
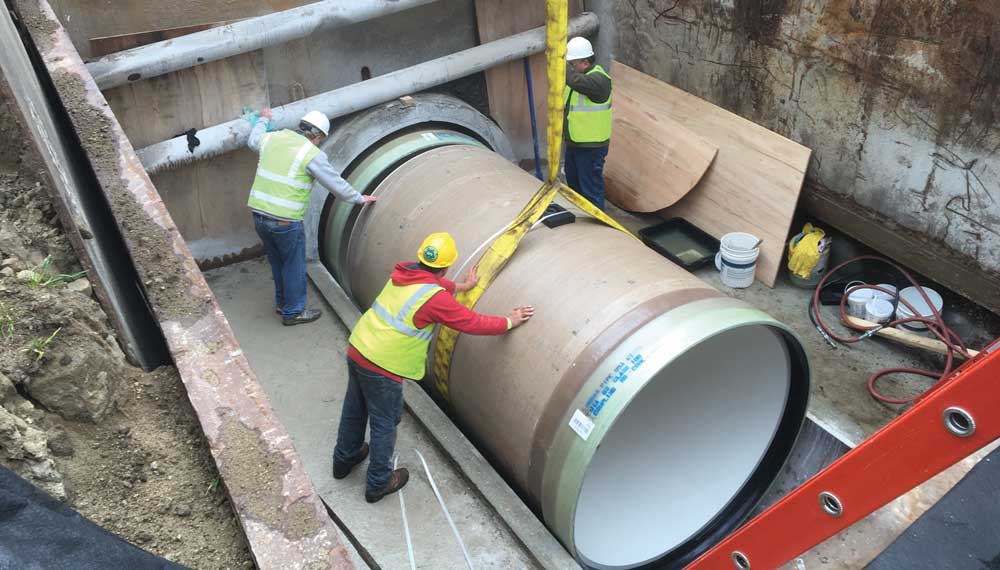
Pipe-Bursting
Pipe-Bursting utilizes a bursting head to eliminate the existing pipe while pulling a new pipe into the void that is left. During this process, upsizing to larger diameters is possible. With the old pipe being destroyed, a completely new pipeline will act in its place. Pipe bursting requires pits at both ends for a proper installation.
- 4″ – 48″
- Fully Structural
- Gravity & Pressure Pipe
- Upsizing Possible
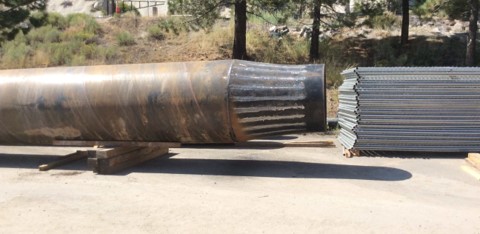
Spray-in-Place Pipe (SIPP)
SIPP involves spraying the interior of a pipeline the entire length with material in order to renew the system. The sprayed material is typically cement, polymer or an epoxy. The installation process uses machinery/robotics to coat the entire pipeline. The internal coating marginally reduces the diameter of the pipe. Since the original pipe wall is to be coated, a heavy cleaning is needed to clear debris and ensure a successful lining.
- 4″ – 200″+
- Gravity & Pressure Pipe
- Minimal ID Loss
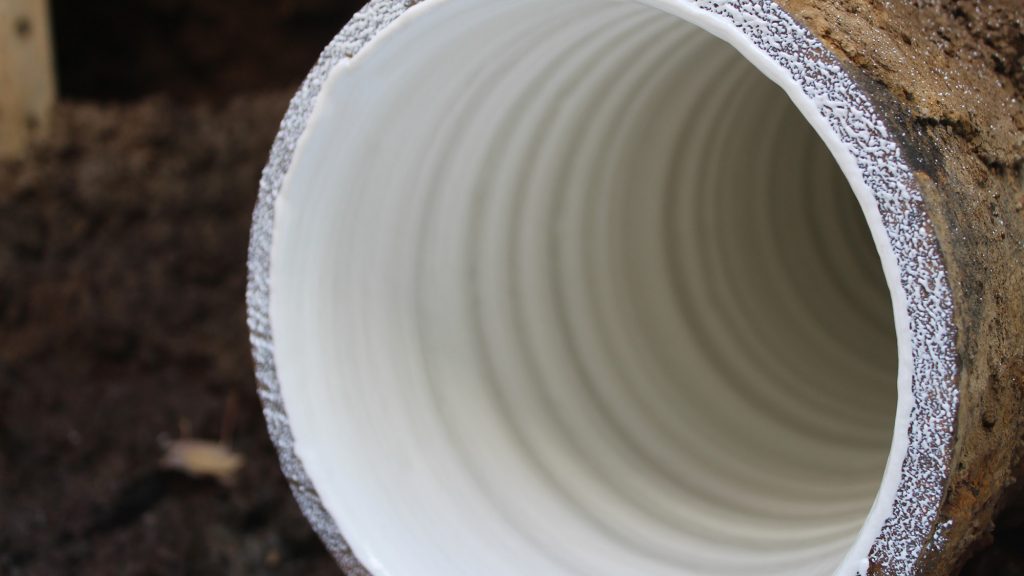
Structural vs. Non-Structural Lining
A fully structural solution forms a singular, stand-alone, pipe that is capable of handling all applied loads (such as soil, surcharge or live loads) within the current system. The finished liner will not need the additional support of the existing line. The goal of this repair solution is to essentially negate the structural reliance for the old pipeline. A structural design adheres to relevant ASTM standards; such as ASTM F1697-18 and ASTM 1741-18 for Spiral Wound and ASTM F1216-16 and ASTM F1743-17 for CIPP.
Nonstructural methods serve as preventative maintenance, or corrosion protection, to an existing pipe, without providing structural support. This includes point or spot repairs that may assist with factors such as hydraulics or corrosion. However, this adds no structural support.
The Typical Trenchless Process
A typical trenchless lining project’s process will vary by the method used, however there are many similarities. Here is an overview for a typical installation:
Pre-Lining
Before lining can take place, the pipe will most likely require a cleaning and inspection. The degree of cleaning depends on the lining method to be used; for instance a SIPP repair will require a heavier cleaning than a pipe-bursting job. The purpose for an inspection is to ensure that the pipeline is ready for rehabilitation and does not need any repairs or adjustments before the new liner is installed.
Inspections are typically carried out by robotic crawlers that have cameras to provide a visual condition assessment of the pipe. There are enhanced inspection methods to get a clearer 3-D image of the pipe as well. These include Sonar Profiling and LiDAR.
Liner Installation
When the pipe is prepared and ready, the liner installation begins. The proper equipment and materials are put in place within the pipeline and the renewal process commences. For Spiral Wound (and most trenchless pipe lining methods) the actual pipe lining can take anywhere from 1 day to several months, depending on the scope of the project and method chosen. The liner is installed whether by inversion (CIPP), mechanical winding (Spiral Wound Lining), insertion (sliplining), or by means of any other method. The Spiral Wound installation process includes:
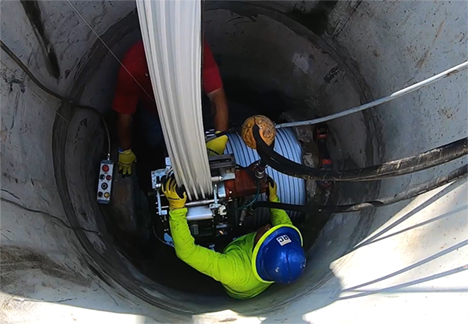
1) Constructing the Liner
Once the machine has been lowered into the manhole/pipeline, a continuous strip of PVC is fed from an above-ground spool directly inside the pipe. The edge of the PVC strip is locked together, forming a liner within the host pipe. If the Spiral Wound method is tight-fitting (6”-60”), no bracing and subsequent grouting is required.
2) Bracing for Grout
If the PVC liner requires the annular space to be filled, bracing is installed within the liner for stability during the grouting process.
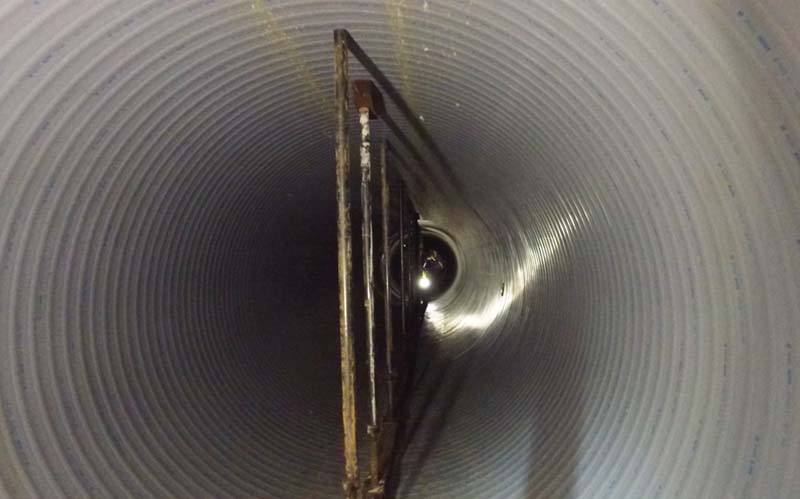
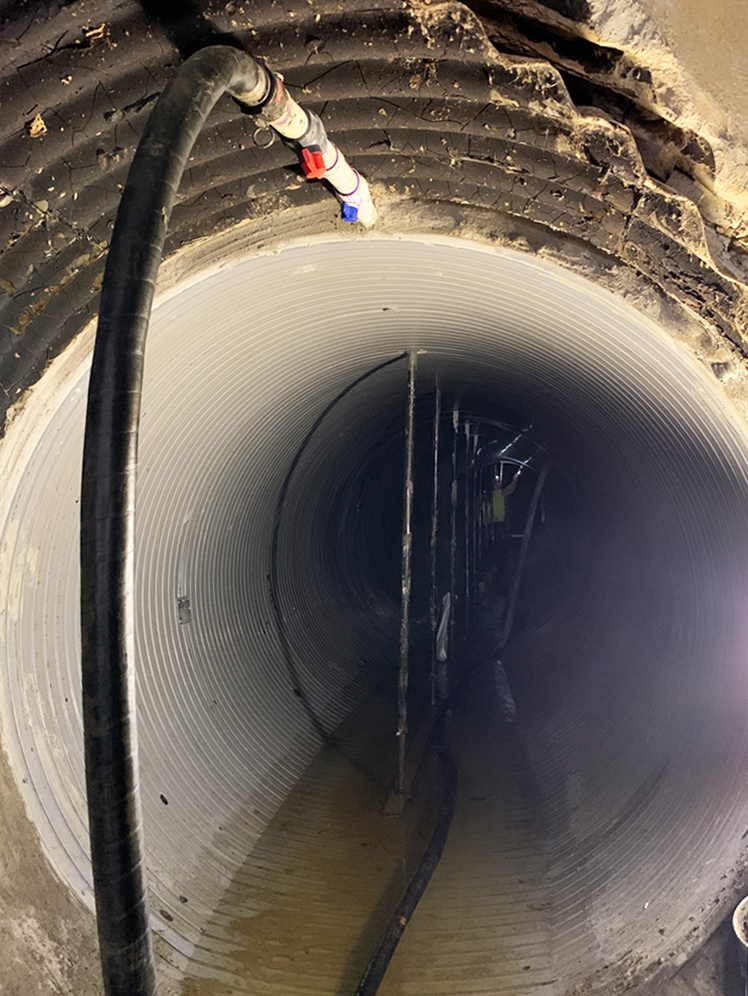
3) Grouting
Grout is injected between the initial pipe and the constructed liner for certain PVC liners. The grout installation takes place through a series of lifts.
4) Sealing the Liner
If the PVC liner is tight-fitting and service connections (if applicable) are reinstated, the installation process involves only steps 1 and 4. All PVC liners are sealed at the termination of the pipe.
Minor traffic disruptions may be present during the installation, as small crews and trucks work out of an access point such as a manhole. Often this leads to single-lane closures, if that, conditional to the lining technology’s above-ground footprint.
Temporary Bypass Pumping
One of the main considerations when dealing with a trenchless rehab project is managing the existing flows during a liner installation. A common solution for the flow is temporary bypass pumping; a process to pump the pipeline’s flow around the section of pipe being renewed. This is often achieved through a pump and piping network, to transport the flow around the repair section. Trenchless rehabilitation technologies that involve curing in the lining process require flow to be pumped around the area of repair. Additionally, many trenchless rehabilitation methods require bypass for larger diameter pipelines, especially those with higher flow levels. In the case of CIPP, certain smaller diameter applications will properly handle flow solely with plugs and no bypass. However, in the instances of longer runs and larger pipes, a bypass pumping operation becomes much more likely.
Equipment and Flow
As part of your plan, you’ll need to consider the peak flow of your pipeline, which is the highest flow level possible with a given day (typically morning or late afternoon). Likewise, another important factor is the total pressure required of the system, or the Total Dynamic Head (TDH). This information will help determine the equipment needed for the temporary bypass. This includes selecting the right type of pump and also the number of pumps required for any particular project. It is not uncommon for projects to have multiple pumps diverting the flow around an area of repair, especially larger diameter pipe rehab projects.
Cost of Temporary Bypass Pumping
Temporary bypass pumping is often vital for CIPP projects; however, it is not inexpensive. We recently conducted an in-house study that is detailed in our white paper, which you can download here. We analyzed 40 CIPP bid tabulations from 25 states, dating from 2015 – 2019. Given these constraints (and others detailed in the paper), the average portion bypass pumping cost was over 15% of the total bid. This percent increased when isolating projects dealing with diameters larger than 20”. For the full results, download our paper.
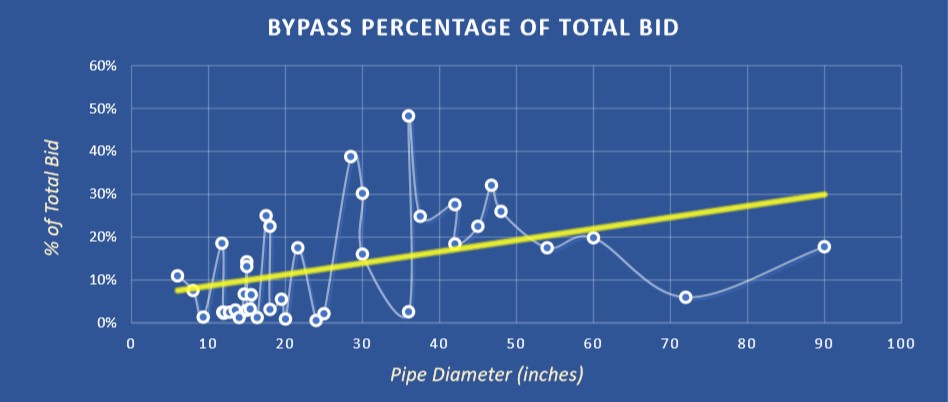
Planning Out Costs
Traditional open-cut construction pricing begins at roughly $250+ per linear foot with the chance of increased price due to additional factors. With the efficiency and non-invasive nature of trenchless lining, the costs associated with these methods are typically cheaper than traditional repair. Trenchless lining projects are roughly $30-1,000 per linear foot of pipe replacement. This wide range of cost depends heavily on a few factors, mainly the diameter and length of the pipe.
Need help planning out a trenchless pipe lining project?
Total Length
Trenchless sewer repair costs are heavily influenced by the length of the pipe. For instance, a longer project will most likely contain lower material costs per linear foot than a shorter project of similar diameter due to scale. Renewing 100 feet of pipe compared to 1,000 feet will yield different dollar amounts within the line items of a project bid. This cost may go up depending on other factors, such as the size, shape, and material of your pipe.
Pipe Size and Shape
The size and shape of your pipe are a major factor in the overall cost. Larger diameter pipelines will typically cost more per linear foot to repair than a smaller pipe. For example, longer runs of pipe under 15” routinely cost below $100 per linear foot for trenchless rehabilitation. The shape of the pipe may also influence the cost of the trenchless sewer repair. With more untraditional piping shapes, it may require additional work to repair the pipe to fit the initial shape. When planning a repair, knowing the size, shape, and type of pipe you’re dealing with can make the project run a little smoother.